Why don't modern jet engines use forced exhaust mixing?Why did Boeing remove the engine chevrons on the 777-X?When is jet engine thrust maximum?How does turbofan engine performance depend on speed and density altutude?Do jet engine exhausts usually glow orange?How does contrail formation differ from turbofan to turbojet?How much thrust is lost due to the bleed air system?What noise reduction measures were taken in the time between hush kits and chevrons?How do aircraft engine manufacturers achieve a higher bypass ratio while still meeting the thrust requirements for a given aircraft?At what Mach Number do variable cycle engines (VCEs) start showing benefits over turbofans?What prevents DC-9 series aircraft from being reengined with more-efficient engines?Why are most turbofans tractors, but most propfans pushers?Does the P&W F100 turbofan engine of the F-16 really produce this much power?
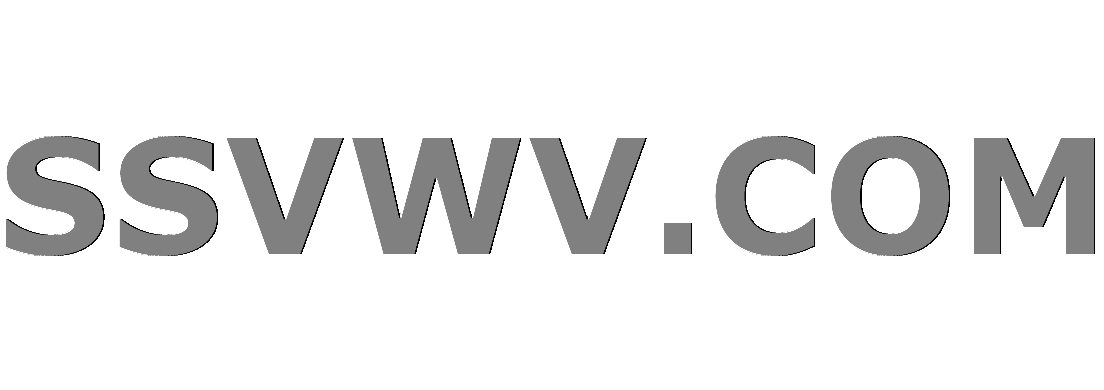
Multi tool use
Go to last file in vim
Is there a fallacy about "appeal to 'big words'"?
Output the list of musical notes
Is the Microsoft recommendation to use C# properties applicable to game development?
If a person claims to know anything could it be disproven by saying 'prove that we are not in a simulation'?
What are the advantages of this gold finger shape?
Locked room poison mystery!
Why do my bicycle brakes get worse and feel more 'squishy" over time?
How to use Palatino font for text and what about maths?
When did Bilbo and Frodo learn that Gandalf was a Maia?
When was "Fredo" an insult to Italian-Americans?
Scam? Phone call from "Department of Social Security" asking me to call back
Why aren't rockets built with truss structures inside their fuel & oxidizer tanks to increase structural strength?
How would armour (and combat) change if the fighter didn't need to actually wear it?
Suspension compromise for urban use
What was the intention with the Commodore 128?
Bringing Power Supplies on Plane?
Is there a word for returning to unpreparedness?
What is the hottest thing in the universe?
Setting up a Mathematical Institute of Refereeing?
Adding things to bunches of things vs multiplication
Is there a name for the technique in songs/poems, where the rhyming pattern primes the listener for a certain line, which never comes?
Telephone number in spoken words
What is axle tramp?
Why don't modern jet engines use forced exhaust mixing?
Why did Boeing remove the engine chevrons on the 777-X?When is jet engine thrust maximum?How does turbofan engine performance depend on speed and density altutude?Do jet engine exhausts usually glow orange?How does contrail formation differ from turbofan to turbojet?How much thrust is lost due to the bleed air system?What noise reduction measures were taken in the time between hush kits and chevrons?How do aircraft engine manufacturers achieve a higher bypass ratio while still meeting the thrust requirements for a given aircraft?At what Mach Number do variable cycle engines (VCEs) start showing benefits over turbofans?What prevents DC-9 series aircraft from being reengined with more-efficient engines?Why are most turbofans tractors, but most propfans pushers?Does the P&W F100 turbofan engine of the F-16 really produce this much power?
.everyoneloves__top-leaderboard:empty,.everyoneloves__mid-leaderboard:empty,.everyoneloves__bot-mid-leaderboard:empty margin-bottom:0;
$begingroup$
Jet engines are noisy[citation needed] - even a modern high-bypass turbofan is still deafeningly loud compared to pretty much anything except the even-louder low-bypass turbofans or a turbojet (much louder still than even a low-bypass turbofan). Unsurprisingly, making jets quieter has been a major concern for the entire jet age; as the majority of a jet engine's noise comes from turbulence at the boundary between the hot core exhaust, on the one hand, and the ambient air (turbojets) / bypass airflow (turbofans), on the other (along with, for turbofans, a small contribution from turbulence at the boundary between the bypass airflow and the ambient air), the primary means of doing this without needing a turbine-incineratingly-high bypass ratio1 is by making it so that the two or three exhaust streams mix smoothly, and preferably do so before going out the tailpipe (so that any noise that is generated during the mixing process can be trapped within the nacelle).
To this end, early jetliners used intricate forced-mixer tailpipes, which were extremely effective at mixing the exhaust and the ambient air, and, thereby, reducing noise; they could either be built into the engine at manufacture time, or retrofitted later on as a "hushkit". These could be seen both on turbojets...2
...and on turbofans.3
With the switch to high-bypass turbofans in the 1970s and 1980s, the dramatically-increased bypass ratio of the new engines was enough all by itself to produce a large drop in noisiness, such that even a plain, unmixed tailpipe was acceptable, and the forced-mixer tailpipes of the earlier engines slowly disappeared from view as the numbers of aircraft using the older engines dwindled.
However, since then, the NIMBYs have gotten more exacting and noise standards have continued to grow stricter and stricter, forcing jets to again use exhaust mixing to make them quieter. Two methods for doing this are in common use:
Chevrons
These sawtoothed tailpipe rims enhance the mixing of the core, bypass, and ambient air, reducing noise:4
Shared tailpipes
These engines simply send both the core and bypass airflow through a single, long tailpipe, where shearing forces at the boundary between the two airstreams create turbulence that causes them to mix to some extent before exiting the engine:5
Both of these methods, however, are fairly inefficient at mixing the different airstreams; a scaled-up forced mixer would be far more mixy (and, therefore, more noise-reducingy). So why do modern high-bypass turbofans still use inefficient methods of exhaust mixing, instead of the more effective forced mixing?
1: A higher bypass ratio requires (for a given thrust rating) more power per unit turbine, which requires the turbine to run hotter.
2: Exhaust mixer of a General Electric CJ805-3 turbojet from a Convair 880 (image by Thomas R. Machnitzki, via DoxTxob at Wikimedia Commons).
3: Exhaust mixer of a Rolls-Royce Conway RCo.12 low-bypass turbofan from a Boeing 707-420 (image by Alf van Beem at Wikimedia Commons).
4: Exhaust mixer of a General Electric GEnx-2B high-bypass turbofan from a Boeing 747-8I (image by Olivier Cleynen at Wikimedia Commons); note the chevrons on both the fan cowling (here opened to appease the peanut gallery), for mixing the bypass airflow with the ambient air, and on the core tailpipe, for mixing the core exhaust with the bypass airflow.
5: Exhaust mixers of two General Electric/SNECMA CFM56-5C high-bypass turbofans from an Airbus A340-300 (image by Hansueli Krapf at Wikimedia Commons); two more A340s, along with their engines and said engines' exhaust mixers, are also visible in the background (one each at upper left and upper far right; please ignore the 747 at upper mid right).
jet-engine airliner noise noise-reduction
$endgroup$
add a comment |
$begingroup$
Jet engines are noisy[citation needed] - even a modern high-bypass turbofan is still deafeningly loud compared to pretty much anything except the even-louder low-bypass turbofans or a turbojet (much louder still than even a low-bypass turbofan). Unsurprisingly, making jets quieter has been a major concern for the entire jet age; as the majority of a jet engine's noise comes from turbulence at the boundary between the hot core exhaust, on the one hand, and the ambient air (turbojets) / bypass airflow (turbofans), on the other (along with, for turbofans, a small contribution from turbulence at the boundary between the bypass airflow and the ambient air), the primary means of doing this without needing a turbine-incineratingly-high bypass ratio1 is by making it so that the two or three exhaust streams mix smoothly, and preferably do so before going out the tailpipe (so that any noise that is generated during the mixing process can be trapped within the nacelle).
To this end, early jetliners used intricate forced-mixer tailpipes, which were extremely effective at mixing the exhaust and the ambient air, and, thereby, reducing noise; they could either be built into the engine at manufacture time, or retrofitted later on as a "hushkit". These could be seen both on turbojets...2
...and on turbofans.3
With the switch to high-bypass turbofans in the 1970s and 1980s, the dramatically-increased bypass ratio of the new engines was enough all by itself to produce a large drop in noisiness, such that even a plain, unmixed tailpipe was acceptable, and the forced-mixer tailpipes of the earlier engines slowly disappeared from view as the numbers of aircraft using the older engines dwindled.
However, since then, the NIMBYs have gotten more exacting and noise standards have continued to grow stricter and stricter, forcing jets to again use exhaust mixing to make them quieter. Two methods for doing this are in common use:
Chevrons
These sawtoothed tailpipe rims enhance the mixing of the core, bypass, and ambient air, reducing noise:4
Shared tailpipes
These engines simply send both the core and bypass airflow through a single, long tailpipe, where shearing forces at the boundary between the two airstreams create turbulence that causes them to mix to some extent before exiting the engine:5
Both of these methods, however, are fairly inefficient at mixing the different airstreams; a scaled-up forced mixer would be far more mixy (and, therefore, more noise-reducingy). So why do modern high-bypass turbofans still use inefficient methods of exhaust mixing, instead of the more effective forced mixing?
1: A higher bypass ratio requires (for a given thrust rating) more power per unit turbine, which requires the turbine to run hotter.
2: Exhaust mixer of a General Electric CJ805-3 turbojet from a Convair 880 (image by Thomas R. Machnitzki, via DoxTxob at Wikimedia Commons).
3: Exhaust mixer of a Rolls-Royce Conway RCo.12 low-bypass turbofan from a Boeing 707-420 (image by Alf van Beem at Wikimedia Commons).
4: Exhaust mixer of a General Electric GEnx-2B high-bypass turbofan from a Boeing 747-8I (image by Olivier Cleynen at Wikimedia Commons); note the chevrons on both the fan cowling (here opened to appease the peanut gallery), for mixing the bypass airflow with the ambient air, and on the core tailpipe, for mixing the core exhaust with the bypass airflow.
5: Exhaust mixers of two General Electric/SNECMA CFM56-5C high-bypass turbofans from an Airbus A340-300 (image by Hansueli Krapf at Wikimedia Commons); two more A340s, along with their engines and said engines' exhaust mixers, are also visible in the background (one each at upper left and upper far right; please ignore the 747 at upper mid right).
jet-engine airliner noise noise-reduction
$endgroup$
add a comment |
$begingroup$
Jet engines are noisy[citation needed] - even a modern high-bypass turbofan is still deafeningly loud compared to pretty much anything except the even-louder low-bypass turbofans or a turbojet (much louder still than even a low-bypass turbofan). Unsurprisingly, making jets quieter has been a major concern for the entire jet age; as the majority of a jet engine's noise comes from turbulence at the boundary between the hot core exhaust, on the one hand, and the ambient air (turbojets) / bypass airflow (turbofans), on the other (along with, for turbofans, a small contribution from turbulence at the boundary between the bypass airflow and the ambient air), the primary means of doing this without needing a turbine-incineratingly-high bypass ratio1 is by making it so that the two or three exhaust streams mix smoothly, and preferably do so before going out the tailpipe (so that any noise that is generated during the mixing process can be trapped within the nacelle).
To this end, early jetliners used intricate forced-mixer tailpipes, which were extremely effective at mixing the exhaust and the ambient air, and, thereby, reducing noise; they could either be built into the engine at manufacture time, or retrofitted later on as a "hushkit". These could be seen both on turbojets...2
...and on turbofans.3
With the switch to high-bypass turbofans in the 1970s and 1980s, the dramatically-increased bypass ratio of the new engines was enough all by itself to produce a large drop in noisiness, such that even a plain, unmixed tailpipe was acceptable, and the forced-mixer tailpipes of the earlier engines slowly disappeared from view as the numbers of aircraft using the older engines dwindled.
However, since then, the NIMBYs have gotten more exacting and noise standards have continued to grow stricter and stricter, forcing jets to again use exhaust mixing to make them quieter. Two methods for doing this are in common use:
Chevrons
These sawtoothed tailpipe rims enhance the mixing of the core, bypass, and ambient air, reducing noise:4
Shared tailpipes
These engines simply send both the core and bypass airflow through a single, long tailpipe, where shearing forces at the boundary between the two airstreams create turbulence that causes them to mix to some extent before exiting the engine:5
Both of these methods, however, are fairly inefficient at mixing the different airstreams; a scaled-up forced mixer would be far more mixy (and, therefore, more noise-reducingy). So why do modern high-bypass turbofans still use inefficient methods of exhaust mixing, instead of the more effective forced mixing?
1: A higher bypass ratio requires (for a given thrust rating) more power per unit turbine, which requires the turbine to run hotter.
2: Exhaust mixer of a General Electric CJ805-3 turbojet from a Convair 880 (image by Thomas R. Machnitzki, via DoxTxob at Wikimedia Commons).
3: Exhaust mixer of a Rolls-Royce Conway RCo.12 low-bypass turbofan from a Boeing 707-420 (image by Alf van Beem at Wikimedia Commons).
4: Exhaust mixer of a General Electric GEnx-2B high-bypass turbofan from a Boeing 747-8I (image by Olivier Cleynen at Wikimedia Commons); note the chevrons on both the fan cowling (here opened to appease the peanut gallery), for mixing the bypass airflow with the ambient air, and on the core tailpipe, for mixing the core exhaust with the bypass airflow.
5: Exhaust mixers of two General Electric/SNECMA CFM56-5C high-bypass turbofans from an Airbus A340-300 (image by Hansueli Krapf at Wikimedia Commons); two more A340s, along with their engines and said engines' exhaust mixers, are also visible in the background (one each at upper left and upper far right; please ignore the 747 at upper mid right).
jet-engine airliner noise noise-reduction
$endgroup$
Jet engines are noisy[citation needed] - even a modern high-bypass turbofan is still deafeningly loud compared to pretty much anything except the even-louder low-bypass turbofans or a turbojet (much louder still than even a low-bypass turbofan). Unsurprisingly, making jets quieter has been a major concern for the entire jet age; as the majority of a jet engine's noise comes from turbulence at the boundary between the hot core exhaust, on the one hand, and the ambient air (turbojets) / bypass airflow (turbofans), on the other (along with, for turbofans, a small contribution from turbulence at the boundary between the bypass airflow and the ambient air), the primary means of doing this without needing a turbine-incineratingly-high bypass ratio1 is by making it so that the two or three exhaust streams mix smoothly, and preferably do so before going out the tailpipe (so that any noise that is generated during the mixing process can be trapped within the nacelle).
To this end, early jetliners used intricate forced-mixer tailpipes, which were extremely effective at mixing the exhaust and the ambient air, and, thereby, reducing noise; they could either be built into the engine at manufacture time, or retrofitted later on as a "hushkit". These could be seen both on turbojets...2
...and on turbofans.3
With the switch to high-bypass turbofans in the 1970s and 1980s, the dramatically-increased bypass ratio of the new engines was enough all by itself to produce a large drop in noisiness, such that even a plain, unmixed tailpipe was acceptable, and the forced-mixer tailpipes of the earlier engines slowly disappeared from view as the numbers of aircraft using the older engines dwindled.
However, since then, the NIMBYs have gotten more exacting and noise standards have continued to grow stricter and stricter, forcing jets to again use exhaust mixing to make them quieter. Two methods for doing this are in common use:
Chevrons
These sawtoothed tailpipe rims enhance the mixing of the core, bypass, and ambient air, reducing noise:4
Shared tailpipes
These engines simply send both the core and bypass airflow through a single, long tailpipe, where shearing forces at the boundary between the two airstreams create turbulence that causes them to mix to some extent before exiting the engine:5
Both of these methods, however, are fairly inefficient at mixing the different airstreams; a scaled-up forced mixer would be far more mixy (and, therefore, more noise-reducingy). So why do modern high-bypass turbofans still use inefficient methods of exhaust mixing, instead of the more effective forced mixing?
1: A higher bypass ratio requires (for a given thrust rating) more power per unit turbine, which requires the turbine to run hotter.
2: Exhaust mixer of a General Electric CJ805-3 turbojet from a Convair 880 (image by Thomas R. Machnitzki, via DoxTxob at Wikimedia Commons).
3: Exhaust mixer of a Rolls-Royce Conway RCo.12 low-bypass turbofan from a Boeing 707-420 (image by Alf van Beem at Wikimedia Commons).
4: Exhaust mixer of a General Electric GEnx-2B high-bypass turbofan from a Boeing 747-8I (image by Olivier Cleynen at Wikimedia Commons); note the chevrons on both the fan cowling (here opened to appease the peanut gallery), for mixing the bypass airflow with the ambient air, and on the core tailpipe, for mixing the core exhaust with the bypass airflow.
5: Exhaust mixers of two General Electric/SNECMA CFM56-5C high-bypass turbofans from an Airbus A340-300 (image by Hansueli Krapf at Wikimedia Commons); two more A340s, along with their engines and said engines' exhaust mixers, are also visible in the background (one each at upper left and upper far right; please ignore the 747 at upper mid right).
jet-engine airliner noise noise-reduction
jet-engine airliner noise noise-reduction
edited 5 hours ago
Sean
asked 8 hours ago


SeanSean
8,1364 gold badges40 silver badges108 bronze badges
8,1364 gold badges40 silver badges108 bronze badges
add a comment |
add a comment |
2 Answers
2
active
oldest
votes
$begingroup$
Source: wikimedia.org
They're back. Above is the General Electric Passport. Entry into service was 2018.
Its core cowling, exhaust cone and mixer are made in ox-ox composites, with inorganic high-temperature-tolerant resins and oxide ceramics CMCs to withstand 1,000°C without deformation, saving weight and allowing complex molding.
The above hints at the hotter exhausts of the newer (since the mixers disappeared) engines, and that CMCs were the solution.
I could not find EGT trend data, and the exhaust temperature contours in airport planning manuals show the temperature after the natural mixing with the massive bypass, but for the turbine inlet temperature, below is the trend:
Source: researchgate.net
An A380 FCOM lists the max continuous EGT as 970°C, while an MD80 FCOM lists it as 580°C (both don't have mixers, but it shows the trend). While you can bleed-cool turbine blades, there must have been no gain in cooling a mixer with bleed or they would have done it (bleed takes away from a combustor's efficiency, and at some point overall gains turn into losses).
Related: Why did Boeing remove the engine chevrons on the 777-X?
$endgroup$
add a comment |
$begingroup$
Why don't modern jet engines use forced exhaust mixing?
Because there isn't as much gain to be achieved from the jet exhaust anymore, and because forced mixing impacts performance.
Gains. From The Jet Engine by Rolls Royce. The text in the lower right corner reads:
A comparison of the noise distribution of two generations of engines. The bubbles approximately indicate the relative size of the main individual engine noise sources and the angular extent indicates where each is most prominent. The noise contributions from a modern turbofan engine are greatly reduced and much more evenly matched than from a turbojet.
- On the left the noise footprint of a typical 1960s engine where by far most of the noise was caused by the jet exhaust. This is where most of the thrust came from - the exhaust exits at Mach 1, at 700 °C over 600 m/s. Huge gains to be made in slowing this down.
- On the right a 1990s generation engine, where the dominant noise source is the fan - this is now where most gains can be made. The jet takes third place, Turbine + Combustion is slightly higher. Overall noise level is significantly lower, since the ear perceives noise logarithmically: two noise sources of 100 dB add up to 103 dB.
Performance impact. From the Wiki page linked in OP:
Hush kits can adversely affect the range and performance of the aircraft they are fitted to because of the extra weight. It also reduces engine performance and aerodynamic efficiency.
The exhaust mixing kit catches some of the generated thrust through friction and back pressure, and is therefore always a performance reducer. The wiki mentions an increase reduction in fuel burn of 0.5% for short trips of the B727.
$endgroup$
add a comment |
Your Answer
StackExchange.ready(function()
var channelOptions =
tags: "".split(" "),
id: "528"
;
initTagRenderer("".split(" "), "".split(" "), channelOptions);
StackExchange.using("externalEditor", function()
// Have to fire editor after snippets, if snippets enabled
if (StackExchange.settings.snippets.snippetsEnabled)
StackExchange.using("snippets", function()
createEditor();
);
else
createEditor();
);
function createEditor()
StackExchange.prepareEditor(
heartbeatType: 'answer',
autoActivateHeartbeat: false,
convertImagesToLinks: false,
noModals: true,
showLowRepImageUploadWarning: true,
reputationToPostImages: null,
bindNavPrevention: true,
postfix: "",
imageUploader:
brandingHtml: "Powered by u003ca class="icon-imgur-white" href="https://imgur.com/"u003eu003c/au003e",
contentPolicyHtml: "User contributions licensed under u003ca href="https://creativecommons.org/licenses/by-sa/3.0/"u003ecc by-sa 3.0 with attribution requiredu003c/au003e u003ca href="https://stackoverflow.com/legal/content-policy"u003e(content policy)u003c/au003e",
allowUrls: true
,
noCode: true, onDemand: true,
discardSelector: ".discard-answer"
,immediatelyShowMarkdownHelp:true
);
);
Sign up or log in
StackExchange.ready(function ()
StackExchange.helpers.onClickDraftSave('#login-link');
);
Sign up using Google
Sign up using Facebook
Sign up using Email and Password
Post as a guest
Required, but never shown
StackExchange.ready(
function ()
StackExchange.openid.initPostLogin('.new-post-login', 'https%3a%2f%2faviation.stackexchange.com%2fquestions%2f67747%2fwhy-dont-modern-jet-engines-use-forced-exhaust-mixing%23new-answer', 'question_page');
);
Post as a guest
Required, but never shown
2 Answers
2
active
oldest
votes
2 Answers
2
active
oldest
votes
active
oldest
votes
active
oldest
votes
$begingroup$
Source: wikimedia.org
They're back. Above is the General Electric Passport. Entry into service was 2018.
Its core cowling, exhaust cone and mixer are made in ox-ox composites, with inorganic high-temperature-tolerant resins and oxide ceramics CMCs to withstand 1,000°C without deformation, saving weight and allowing complex molding.
The above hints at the hotter exhausts of the newer (since the mixers disappeared) engines, and that CMCs were the solution.
I could not find EGT trend data, and the exhaust temperature contours in airport planning manuals show the temperature after the natural mixing with the massive bypass, but for the turbine inlet temperature, below is the trend:
Source: researchgate.net
An A380 FCOM lists the max continuous EGT as 970°C, while an MD80 FCOM lists it as 580°C (both don't have mixers, but it shows the trend). While you can bleed-cool turbine blades, there must have been no gain in cooling a mixer with bleed or they would have done it (bleed takes away from a combustor's efficiency, and at some point overall gains turn into losses).
Related: Why did Boeing remove the engine chevrons on the 777-X?
$endgroup$
add a comment |
$begingroup$
Source: wikimedia.org
They're back. Above is the General Electric Passport. Entry into service was 2018.
Its core cowling, exhaust cone and mixer are made in ox-ox composites, with inorganic high-temperature-tolerant resins and oxide ceramics CMCs to withstand 1,000°C without deformation, saving weight and allowing complex molding.
The above hints at the hotter exhausts of the newer (since the mixers disappeared) engines, and that CMCs were the solution.
I could not find EGT trend data, and the exhaust temperature contours in airport planning manuals show the temperature after the natural mixing with the massive bypass, but for the turbine inlet temperature, below is the trend:
Source: researchgate.net
An A380 FCOM lists the max continuous EGT as 970°C, while an MD80 FCOM lists it as 580°C (both don't have mixers, but it shows the trend). While you can bleed-cool turbine blades, there must have been no gain in cooling a mixer with bleed or they would have done it (bleed takes away from a combustor's efficiency, and at some point overall gains turn into losses).
Related: Why did Boeing remove the engine chevrons on the 777-X?
$endgroup$
add a comment |
$begingroup$
Source: wikimedia.org
They're back. Above is the General Electric Passport. Entry into service was 2018.
Its core cowling, exhaust cone and mixer are made in ox-ox composites, with inorganic high-temperature-tolerant resins and oxide ceramics CMCs to withstand 1,000°C without deformation, saving weight and allowing complex molding.
The above hints at the hotter exhausts of the newer (since the mixers disappeared) engines, and that CMCs were the solution.
I could not find EGT trend data, and the exhaust temperature contours in airport planning manuals show the temperature after the natural mixing with the massive bypass, but for the turbine inlet temperature, below is the trend:
Source: researchgate.net
An A380 FCOM lists the max continuous EGT as 970°C, while an MD80 FCOM lists it as 580°C (both don't have mixers, but it shows the trend). While you can bleed-cool turbine blades, there must have been no gain in cooling a mixer with bleed or they would have done it (bleed takes away from a combustor's efficiency, and at some point overall gains turn into losses).
Related: Why did Boeing remove the engine chevrons on the 777-X?
$endgroup$
Source: wikimedia.org
They're back. Above is the General Electric Passport. Entry into service was 2018.
Its core cowling, exhaust cone and mixer are made in ox-ox composites, with inorganic high-temperature-tolerant resins and oxide ceramics CMCs to withstand 1,000°C without deformation, saving weight and allowing complex molding.
The above hints at the hotter exhausts of the newer (since the mixers disappeared) engines, and that CMCs were the solution.
I could not find EGT trend data, and the exhaust temperature contours in airport planning manuals show the temperature after the natural mixing with the massive bypass, but for the turbine inlet temperature, below is the trend:
Source: researchgate.net
An A380 FCOM lists the max continuous EGT as 970°C, while an MD80 FCOM lists it as 580°C (both don't have mixers, but it shows the trend). While you can bleed-cool turbine blades, there must have been no gain in cooling a mixer with bleed or they would have done it (bleed takes away from a combustor's efficiency, and at some point overall gains turn into losses).
Related: Why did Boeing remove the engine chevrons on the 777-X?
edited 6 hours ago
answered 7 hours ago


ymb1ymb1
77.9k9 gold badges252 silver badges421 bronze badges
77.9k9 gold badges252 silver badges421 bronze badges
add a comment |
add a comment |
$begingroup$
Why don't modern jet engines use forced exhaust mixing?
Because there isn't as much gain to be achieved from the jet exhaust anymore, and because forced mixing impacts performance.
Gains. From The Jet Engine by Rolls Royce. The text in the lower right corner reads:
A comparison of the noise distribution of two generations of engines. The bubbles approximately indicate the relative size of the main individual engine noise sources and the angular extent indicates where each is most prominent. The noise contributions from a modern turbofan engine are greatly reduced and much more evenly matched than from a turbojet.
- On the left the noise footprint of a typical 1960s engine where by far most of the noise was caused by the jet exhaust. This is where most of the thrust came from - the exhaust exits at Mach 1, at 700 °C over 600 m/s. Huge gains to be made in slowing this down.
- On the right a 1990s generation engine, where the dominant noise source is the fan - this is now where most gains can be made. The jet takes third place, Turbine + Combustion is slightly higher. Overall noise level is significantly lower, since the ear perceives noise logarithmically: two noise sources of 100 dB add up to 103 dB.
Performance impact. From the Wiki page linked in OP:
Hush kits can adversely affect the range and performance of the aircraft they are fitted to because of the extra weight. It also reduces engine performance and aerodynamic efficiency.
The exhaust mixing kit catches some of the generated thrust through friction and back pressure, and is therefore always a performance reducer. The wiki mentions an increase reduction in fuel burn of 0.5% for short trips of the B727.
$endgroup$
add a comment |
$begingroup$
Why don't modern jet engines use forced exhaust mixing?
Because there isn't as much gain to be achieved from the jet exhaust anymore, and because forced mixing impacts performance.
Gains. From The Jet Engine by Rolls Royce. The text in the lower right corner reads:
A comparison of the noise distribution of two generations of engines. The bubbles approximately indicate the relative size of the main individual engine noise sources and the angular extent indicates where each is most prominent. The noise contributions from a modern turbofan engine are greatly reduced and much more evenly matched than from a turbojet.
- On the left the noise footprint of a typical 1960s engine where by far most of the noise was caused by the jet exhaust. This is where most of the thrust came from - the exhaust exits at Mach 1, at 700 °C over 600 m/s. Huge gains to be made in slowing this down.
- On the right a 1990s generation engine, where the dominant noise source is the fan - this is now where most gains can be made. The jet takes third place, Turbine + Combustion is slightly higher. Overall noise level is significantly lower, since the ear perceives noise logarithmically: two noise sources of 100 dB add up to 103 dB.
Performance impact. From the Wiki page linked in OP:
Hush kits can adversely affect the range and performance of the aircraft they are fitted to because of the extra weight. It also reduces engine performance and aerodynamic efficiency.
The exhaust mixing kit catches some of the generated thrust through friction and back pressure, and is therefore always a performance reducer. The wiki mentions an increase reduction in fuel burn of 0.5% for short trips of the B727.
$endgroup$
add a comment |
$begingroup$
Why don't modern jet engines use forced exhaust mixing?
Because there isn't as much gain to be achieved from the jet exhaust anymore, and because forced mixing impacts performance.
Gains. From The Jet Engine by Rolls Royce. The text in the lower right corner reads:
A comparison of the noise distribution of two generations of engines. The bubbles approximately indicate the relative size of the main individual engine noise sources and the angular extent indicates where each is most prominent. The noise contributions from a modern turbofan engine are greatly reduced and much more evenly matched than from a turbojet.
- On the left the noise footprint of a typical 1960s engine where by far most of the noise was caused by the jet exhaust. This is where most of the thrust came from - the exhaust exits at Mach 1, at 700 °C over 600 m/s. Huge gains to be made in slowing this down.
- On the right a 1990s generation engine, where the dominant noise source is the fan - this is now where most gains can be made. The jet takes third place, Turbine + Combustion is slightly higher. Overall noise level is significantly lower, since the ear perceives noise logarithmically: two noise sources of 100 dB add up to 103 dB.
Performance impact. From the Wiki page linked in OP:
Hush kits can adversely affect the range and performance of the aircraft they are fitted to because of the extra weight. It also reduces engine performance and aerodynamic efficiency.
The exhaust mixing kit catches some of the generated thrust through friction and back pressure, and is therefore always a performance reducer. The wiki mentions an increase reduction in fuel burn of 0.5% for short trips of the B727.
$endgroup$
Why don't modern jet engines use forced exhaust mixing?
Because there isn't as much gain to be achieved from the jet exhaust anymore, and because forced mixing impacts performance.
Gains. From The Jet Engine by Rolls Royce. The text in the lower right corner reads:
A comparison of the noise distribution of two generations of engines. The bubbles approximately indicate the relative size of the main individual engine noise sources and the angular extent indicates where each is most prominent. The noise contributions from a modern turbofan engine are greatly reduced and much more evenly matched than from a turbojet.
- On the left the noise footprint of a typical 1960s engine where by far most of the noise was caused by the jet exhaust. This is where most of the thrust came from - the exhaust exits at Mach 1, at 700 °C over 600 m/s. Huge gains to be made in slowing this down.
- On the right a 1990s generation engine, where the dominant noise source is the fan - this is now where most gains can be made. The jet takes third place, Turbine + Combustion is slightly higher. Overall noise level is significantly lower, since the ear perceives noise logarithmically: two noise sources of 100 dB add up to 103 dB.
Performance impact. From the Wiki page linked in OP:
Hush kits can adversely affect the range and performance of the aircraft they are fitted to because of the extra weight. It also reduces engine performance and aerodynamic efficiency.
The exhaust mixing kit catches some of the generated thrust through friction and back pressure, and is therefore always a performance reducer. The wiki mentions an increase reduction in fuel burn of 0.5% for short trips of the B727.
edited 3 hours ago
answered 3 hours ago
KoyovisKoyovis
35.4k9 gold badges93 silver badges188 bronze badges
35.4k9 gold badges93 silver badges188 bronze badges
add a comment |
add a comment |
Thanks for contributing an answer to Aviation Stack Exchange!
- Please be sure to answer the question. Provide details and share your research!
But avoid …
- Asking for help, clarification, or responding to other answers.
- Making statements based on opinion; back them up with references or personal experience.
Use MathJax to format equations. MathJax reference.
To learn more, see our tips on writing great answers.
Sign up or log in
StackExchange.ready(function ()
StackExchange.helpers.onClickDraftSave('#login-link');
);
Sign up using Google
Sign up using Facebook
Sign up using Email and Password
Post as a guest
Required, but never shown
StackExchange.ready(
function ()
StackExchange.openid.initPostLogin('.new-post-login', 'https%3a%2f%2faviation.stackexchange.com%2fquestions%2f67747%2fwhy-dont-modern-jet-engines-use-forced-exhaust-mixing%23new-answer', 'question_page');
);
Post as a guest
Required, but never shown
Sign up or log in
StackExchange.ready(function ()
StackExchange.helpers.onClickDraftSave('#login-link');
);
Sign up using Google
Sign up using Facebook
Sign up using Email and Password
Post as a guest
Required, but never shown
Sign up or log in
StackExchange.ready(function ()
StackExchange.helpers.onClickDraftSave('#login-link');
);
Sign up using Google
Sign up using Facebook
Sign up using Email and Password
Post as a guest
Required, but never shown
Sign up or log in
StackExchange.ready(function ()
StackExchange.helpers.onClickDraftSave('#login-link');
);
Sign up using Google
Sign up using Facebook
Sign up using Email and Password
Sign up using Google
Sign up using Facebook
Sign up using Email and Password
Post as a guest
Required, but never shown
Required, but never shown
Required, but never shown
Required, but never shown
Required, but never shown
Required, but never shown
Required, but never shown
Required, but never shown
Required, but never shown
q,hsiu nySTQ2fcpq,wfpHj zK0kpZCpK70PS 0KLdiWIkaKs2Y,6 JDX9VExpn